Have you ever been woken up in the early morning by construction construction noise outside or just wondered why crews are already hard at work while you are on your morning commute. For the construction industry the typical work hours are from 7:00 am to 3:30 pm. With a 30 minute lunch break, this makes for an 8 hour work day. Although these are typical hours, site conditions and day to day activities can call for an earlier start time.
There are many reasons why construction workers start so early including:
- Maximize the use of daylight
- Miss the heat of the day in the afternoon
- Adjust work hours based on season weather patterns
- Allow for multiple shifts to work onsite
- Miss the morning and evening commuter traffic
- To ensure available parking in downtown work sites
- Avoid impacting regular business when working in occupied buildings
Maximize the use of Daylight
It should be no surprise that the number 1 reason for starting construction work early is to maximize the use of daylight. In Houston in the Winter, for example, the sun rises at around 7 am and sets around 5:30 pm. Starting work at 6:30 am allows for the crews to perform all their Pre-Task Planning, Toolbox Talks, Stretch and Flex, Tool Inspections, and any other morning start activities just before the sun comes up and once that is complete they can hit the ground running and not have to rely on temporary site lighting. If you have ever had to work by a temporary lighting setup than you know the difficulties this can bring and how it can make the site relatively unsafe and increase risk to all employees.
If the crews plan for a normal 8 hour day from 6:30 am to 3:00 pm, and any problems arise onsite that needs to be addressed right away then the early start gives the crews a couple extra hours of daylight at the end of their regular work day to make any fixes. This can help with not leaving the site in a unsafe manner at the end of the day or simply remaining on schedule even when unforeseen events pop up.
In the Northern United States, there is a shortened construction season as the Winter weather and frozen ground forces a lot of construction activities to stop. They tend to overcome this by working longer hours in the summer time to make up for the shortened year. In order to work the longer hours they have to start before the sun rises and finish as it is setting.
Miss the heat of the day
Trying to miss the heat of the day could be one of the more obvious reasons for starting construction so early in the morning. In the south and in Texas, where I live, it gets hot (sometimes very hot) in the summer afternoons, and starting early in the morning helps to take advantage of the cooler morning temperatures. This is not only a comfort thing but can be a serious safety hazard for construction workers. The Center for Construction Research and Training cites that 17 construction workers died in 2015 from heat related illnesses. OSHA’s Hierarchy of Controls shows that the most effective method of hazard prevention is to Eliminate the Hazard.
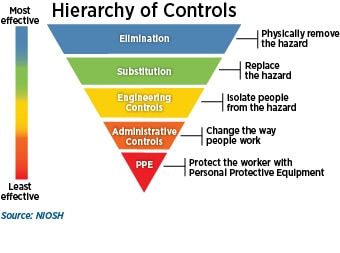
While construction sites will do what they can to protect the employees by introducing engineering and administrative controls such as canopy shades or mandating water breaks, this can only go so far. Eliminating the heat hazard by starting work at 5 or 6 am and finishing by 1 or 2 pm is the most effective safety control there is.
I oversaw a heavy welding project in Southern Georgia which ran through the summer. Due to welding hoods and the heavy PPE required for welders, we opted to start this work at 3 am for the sole purpose of being done before the summer sun started to bake. We were done with work around lunch time before things really started to heat up.
Early morning concrete pours are also not uncommon on job sites for a few reasons. First regardless of the season or weather, there is far less traffic at 4 am that could hold up a ready-mix concrete truck delivery. Typically a concrete load must be placed within about 1.5 to 2 hours of being batched or the concrete starts to set up. This time is eaten up by drive time, queue time onsite, pumping time, and placing time. If there is heavy traffic and possibly even a wreck, then the likelihood of having to discard the truck goes up.
Secondly, the ideal temperature range for pouring concrete is 40 to 90 deg F. Concrete cures through a chemical process called hydration where the water reacts with the cement. This is when the concrete starts to harden and the chemical reaction produces a good deal of heat. Higher ambient temperature speeds up the hydration process and the concrete cures too quickly which can lead to cracking. Conversely, in cooler temperatures the concrete sets slower and is easier to pour and work. Once the ambient temperature rises above 100 F it can flash set and makes finishing near impossible. Admixtures can be added to the batch but this will increase the cost of the mix.
Adjust work hours based on seasonal weather patterns
Starting work early can also help adjust for seasonal weather patterns such as afternoon rains. For example, in Florida they experience many afternoon thunderstorms which if not planned into the work can create construction delays and other scheduling and logistical headaches. By starting work early the site can plan for the expected thunderstorm by either being finished with work before it starts or at a break point, so that work can commence after the storm passes through.
Allow for multiple shifts onsite
A casual passerby may just notice that construction work never seems to stop with work going on 16 or sometimes even 24 hours a day. This is however a carefully orchestrated and scheduled exercise. Sometimes it makes sense to maintain a tight schedule to work 2 or even 3 shifts on site. In order to make this happen some crews will inevitably be working early morning.
Miss the morning and evening commuter traffic
Just like the concrete trucks wanting to miss heavy commuter traffic, so do the actual construction workers. Shifting work hours to be earlier than the typical 8 to 5 employee allows for them to drive in before everyone else is up and also leave to get home before the 5 o’clock crowds are leaving work. The project I am currently working on in South Houston just changed from a 7 am start to a 6 am start as so many workers were driving from all over the city and moving up the start time cut everyone’s commute time in half both ways.
Many construction crews end up working overtime to stay on schedule, so even when working long hours, say from 5 am to 4 pm (10 hours with a 30 minute lunch and two 15 minute breaks), they can still be on the road before the rush hour. This helps them make it home in time to have some family time or even coach their kid’s sports teams.
Ensure available parking in downtown work sites
Having managed a couple projects in downtown Austin, I can attest to how crazy limited the parking options are. While many contractors choose to purchase monthly parking permits for the crews, there are not a lot of affordable options so those reserved spots tend to go to the Project Managers/ Engineers, Superintendents, and Foremen. Therefore street parking and paying the parking meters becomes the go-to choice for the workers. This too is a limited resource so many job sites have opted to start construction even earlier (about 6am) to be beat the normal 7am start crowd and the office workers.
The city has tried to combat the fact that all the street spots are filled by construction vehicles by 7 am and therefore leave nothing available to normal business or tourists. They enacted city ordinances that a vehicle could not be in the same street parking spot for more than 3 hours, even if the parking meter was constantly being fed. This led to complete job sites walking out a few times a day to play musical chairs with their parking spots and trying to find a new curb spot.
Avoid impacting regular business in an occupied building
While there are times when construction activities (or at least those noise making ones) are prohibited by a noise ordinance until after a certain time in the morning, there are also times when it may be required to work nights or early morning as to not impact regular business activities.
For example, I managed a tenant finishout project in an occupied high rise building. Activites such as core drilling through the slabs or hammerdrilling in embeds for all thread hangers had to occur before 7 am because the sound of that work would resonate through the structure floors above and below. So we shifted our start time to 5:30 am. This gave roughly 30 minutes for job start activities and a full hour to hammer drill embeds. We would basically put in all the embeds needed for that days worth of work and then do it again tomorrow.
This specific project example actually had a few reasons why the early start time made sense. Obviously the noise issues just described but also the project was in Downtown Austin so getting in early also beat the commuter traffic and allowed the contractors to find parking spots.